What is Porosity in Welding: Vital Tips for Achieving Flawless Welds
What is Porosity in Welding: Vital Tips for Achieving Flawless Welds
Blog Article
The Scientific Research Behind Porosity: A Comprehensive Overview for Welders and Fabricators
Understanding the complex systems behind porosity in welding is vital for welders and fabricators aiming for impressive workmanship. From the composition of the base materials to the complexities of the welding procedure itself, a plethora of variables conspire to either exacerbate or ease the visibility of porosity.
Understanding Porosity in Welding
FIRST SENTENCE:
Assessment of porosity in welding discloses vital understandings right into the stability and quality of the weld joint. Porosity, defined by the existence of tooth cavities or spaces within the weld metal, is an usual concern in welding processes. These voids, otherwise effectively attended to, can jeopardize the architectural honesty and mechanical homes of the weld, leading to prospective failings in the ended up item.
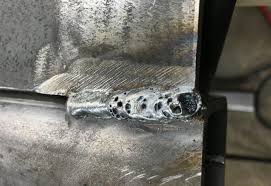
To find and measure porosity, non-destructive testing approaches such as ultrasonic screening or X-ray assessment are typically employed. These techniques permit the recognition of internal defects without endangering the stability of the weld. By examining the size, form, and distribution of porosity within a weld, welders can make informed choices to enhance their welding procedures and accomplish sounder weld joints.
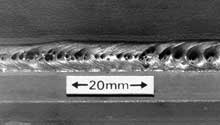
Factors Affecting Porosity Development
The event of porosity in welding is influenced by a myriad of factors, ranging from gas securing effectiveness to the ins and outs of welding criterion settings. Welding specifications, consisting of voltage, current, travel rate, and electrode kind, also effect porosity development. The welding strategy employed, such as gas metal arc welding (GMAW) or protected steel arc welding (SMAW), can affect porosity formation due to variations in warm circulation and gas insurance coverage - What is Porosity.
Impacts of Porosity on Weld High Quality
The visibility of porosity also deteriorates the weld's resistance to rust, as the trapped air or gases within the gaps can respond with the surrounding atmosphere, leading to degradation over time. Furthermore, porosity can hinder the weld's ability to stand up to pressure or influence, additional jeopardizing the total high quality and dependability of the bonded structure. In crucial applications such as aerospace, vehicle, or structural buildings, where safety and security and longevity are paramount, the destructive my response impacts of porosity on weld high quality can have serious effects, emphasizing the relevance of minimizing porosity via correct welding techniques and treatments.
Strategies to Decrease Porosity
Furthermore, making use of the appropriate welding parameters, such as the appropriate voltage, present, and travel rate, is crucial in preventing porosity. Maintaining a constant arc length and angle during welding likewise assists decrease the possibility of porosity.

Moreover, picking the appropriate securing gas and keeping correct gas circulation prices are necessary in lessening porosity. Utilizing the ideal welding strategy, such as back-stepping or using a weaving movement, can likewise help distribute warm uniformly and decrease the possibilities of porosity formation. Lastly, ensuring appropriate ventilation in the welding atmosphere to get rid of any kind of prospective sources of contamination is vital for look here attaining porosity-free welds. By executing these methods, welders can efficiently reduce porosity and produce top notch welded joints.
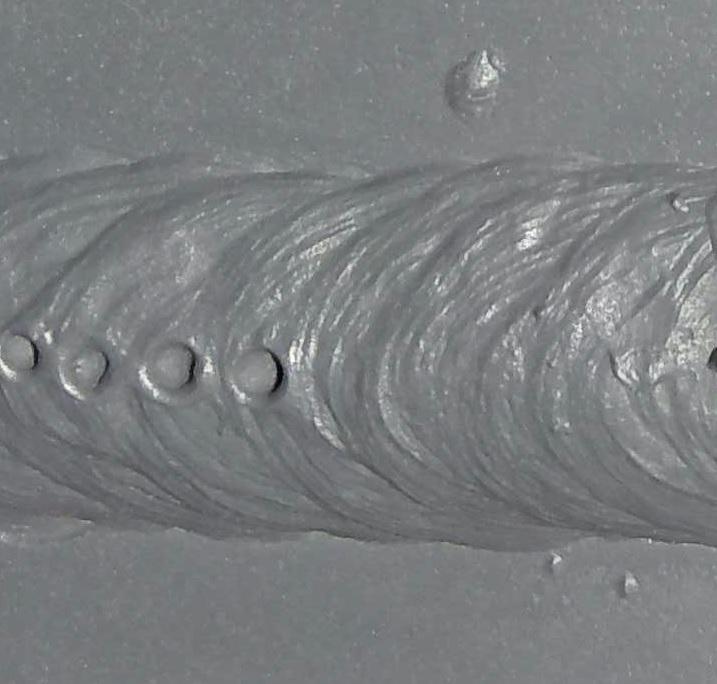
Advanced Solutions for Porosity Control
Carrying out cutting-edge innovations and ingenious approaches plays a critical duty in attaining premium control over porosity in welding processes. One sophisticated service is making use of sophisticated gas mixtures. Securing gases like helium or a mix of argon and hydrogen can aid decrease porosity by giving much better arc security and improved gas insurance coverage. Furthermore, employing sophisticated welding techniques such as pulsed MIG welding or customized ambience welding can also aid reduce porosity concerns.
An additional innovative solution includes using innovative welding equipment. For example, using tools with integrated great post to read attributes like waveform control and sophisticated power resources can enhance weld quality and decrease porosity dangers. Additionally, the application of automated welding systems with accurate control over specifications can dramatically decrease porosity issues.
Additionally, integrating sophisticated monitoring and evaluation technologies such as real-time X-ray imaging or automated ultrasonic testing can help in finding porosity early in the welding procedure, permitting for immediate restorative actions. In general, incorporating these innovative options can significantly enhance porosity control and enhance the general high quality of welded parts.
Final Thought
In verdict, understanding the scientific research behind porosity in welding is vital for welders and fabricators to create top quality welds - What is Porosity. Advanced remedies for porosity control can additionally enhance the welding procedure and guarantee a strong and reliable weld.
Report this page